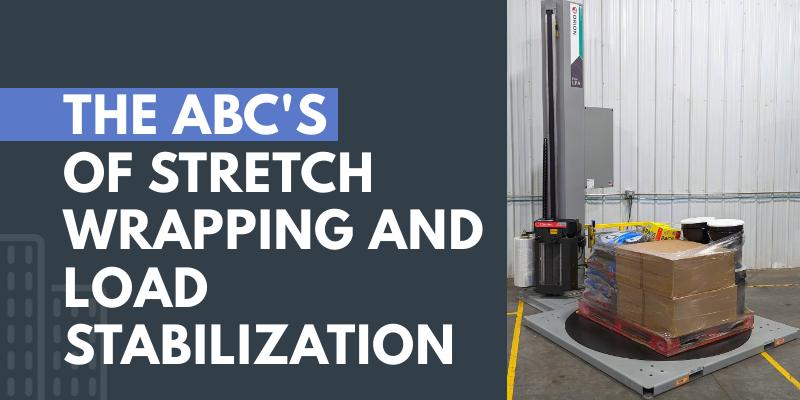
Wrapping a pallet is the last step in securing your product for shipping, and proper technique at the stretch wrapper is crucial to making sure you don’t trip right at the finish line. That technique starts with understanding the load you’re wrapping.
The industry breaks pallets down into three load categories: A, B, and C. Each one has different nuances that can impact the method in which it’s packaged.
A-Type Loads
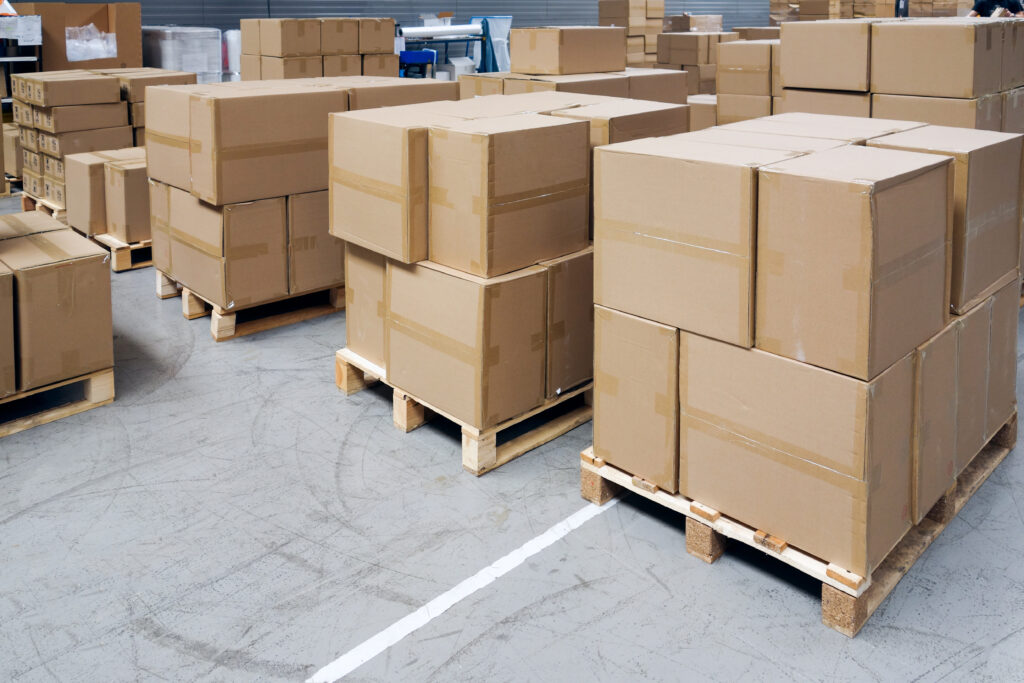
A-type loads are by far the easiest to stretch wrap. The pallets are often stacked in columns or interlocking packages, and the products are heavy enough to be stable when spun.
With these loads, the work to ensure product stays where it needs to is already done. Pallets can be spun around as film is applied to efficiently wrap and prepare them for shipping.
B-Type Loads
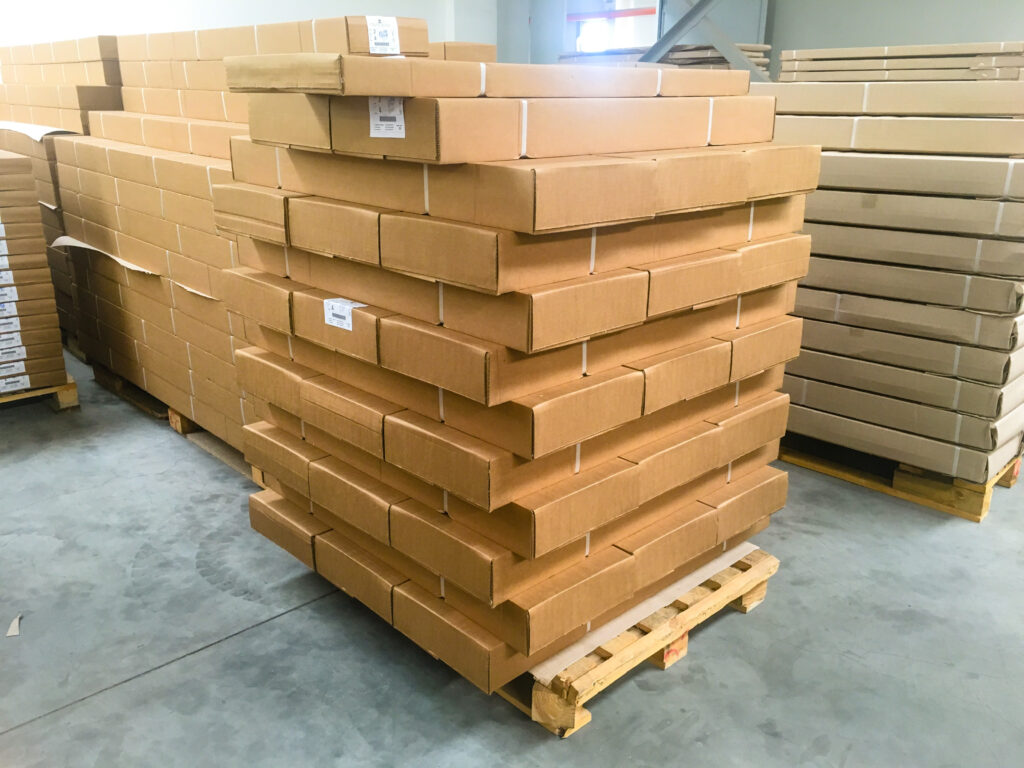
Like A-type, B-type loads can be spun without major issues. However, the speed may need to be lowered slightly and the monitoring from an operator should be more hands-on.
B-type loads are categorized by still being stable but presenting more of a spill risk than A-type. The product may be lighter, the boxes may be less uniform, or there may be other factors that contribute to these pallets presenting a bit more of a challenge. Luckily, with a few minor precautions in place, B-type loads can still be securely spun around a film wrapper without any cause for concern.
C-Type Loads
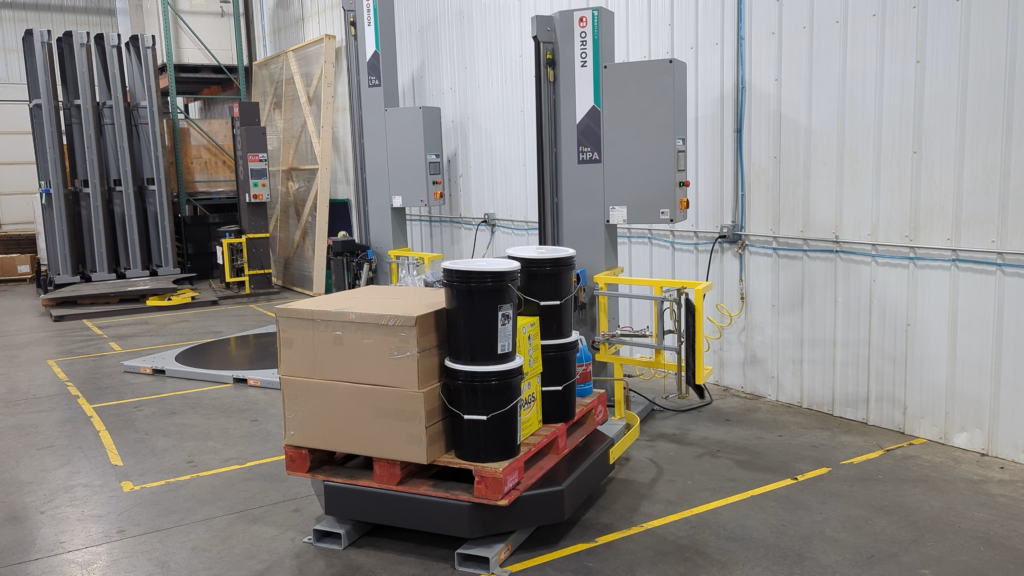
To be considered C-type, a pallet of goods must be very unstable, either from light products, such as tissues, or highly inconsistent packages. If a C-type load is spun at the same speed as A- or B-type without securing measures put in place, product will most likely fall off the pallet.
The first step in dealing with these loads is identifying any weak spots. A common misconception is that only the top or bottom of a load is prone to movement, but shifts can occur anywhere in a stack. By simulating movement with a test load, you can identify where product is most likely to slide during acceleration, rapid stops, swerves, or any of the other potential disruptions that come during transit.
One way to ensure the weak spots don’t cause issues is to start the wrapping at a much slower rate with a focus on problem areas until the items are secured. At that point, the system can speed up, so time is not lost. Orion machines come with a standard “unstable mode” in the HMI system precisely for these applications. Operators can program in the initial RPM and both the instance and rate of any increase in speed. This allows them to properly wrap a C-type load with the push of a button instead of manually handling the spin rate. For these cases, I would also recommend using 30” carriages instead of 20” to apply more film and allow the load to be stabilized faster.
Another option for operators is a rotary arm system, which spins film around the pallet instead of the pallet around the film. While these machines have a higher footprint than turntable or tower systems, they can be worth the space for applications with primarily C-type loads.
Whether you wrap A, B, C, or any combination of the three, an Orion representative can help you determine what stretch wrapping apparatus is the best fit for you and your product. Contact us today to find a machine that secures your load with the efficiency to keep up with your business.
Craig Zelasko is a Regional Sales Manager at Orion (www.orionpackaging.com). He can be reached at Craig.zelasko@promachbuilt.com