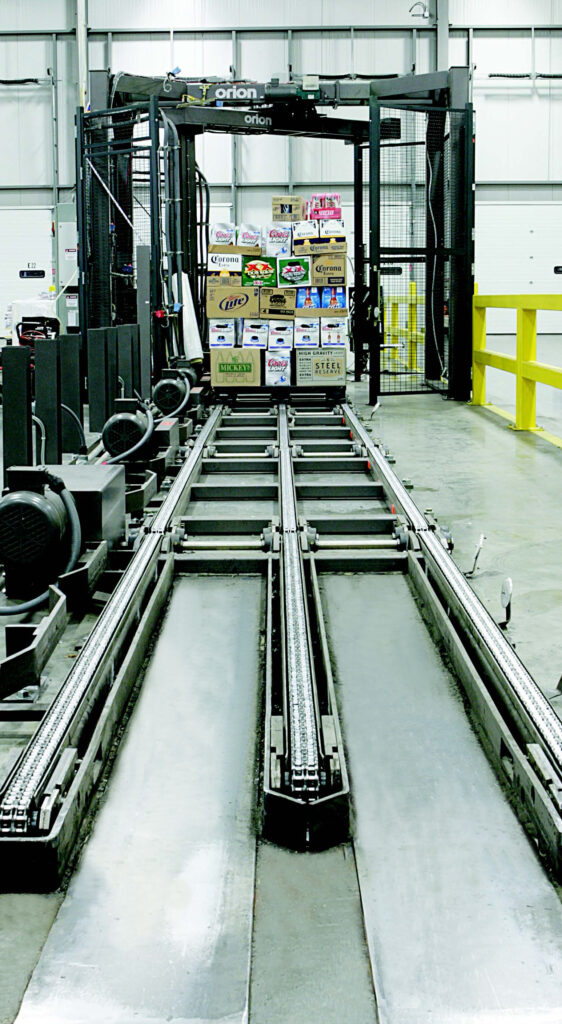
A critical point of a pallet wrapping system is the conveyor. It transports large, heavy, or unwieldy loads safely from a hand-powered pallet jack (also called “walkies”) or forklift to the stretch wrapper. Often the pallets hold stacked boxes of varying sizes, weights, and dimensions, so the conveyor must ensure safe and stable transport.
In the beverage industry, full pallets are often transported in the warehouse with walkies to minimize jostling and shaking. The companion to this is a good conveyor system that maintains a smooth and steady pace of pallets to achieve maximum efficiency.
Part of an efficient conveyor system is one that minimizes unnecessary challenges for the walkie operator. When a conveyor is raised off the ground and requires a ramp to load the pallet, it can become a hazard. The operator must guide a full pallet up an incline, trying to steady it in the process. This can result in load spills that lead to damaged products and potential danger to the operator.
A way to solve this problem is to eliminate the ramp.
One option is a low-profile, automated conveyor that stands just inches off the floor, so there is need for a ramp. It is easier and safer for the operator to bring the load to the infeed zone and then simply lower it onto the conveyor. This smooth transfer helps maintain package stability, protecting the product and the operator.
Once the pallet is on the conveyor, it’s important not only to maintain that stability but also to minimize choppy movements. In applications like beverage distribution centers, where a variety of package sizes create less-stable loads that are more likely to shift, the conveyor needs to operate smoothly. One way to ensure smooth conveyance is with a conveyor that uses an automated three-strand drag chain instead of rollers. Rollers inherently create vibration which can affect the stability of the products. Eliminating rollers maintains the integrity of the stacked pallet, reducing load spills thus improving productivity and increasing output.
Another way to increase productivity is with a conveyor that can move pallets at high speeds. An effective conveyor can move up to 60 feet per minute, as well as handle multiple pallets simultaneously. This allows larger quantities to move through the system, increasing output and positively affecting the bottom line.
Finally, a pallet wrapping system is only as effective as the quality of its material. Conveyors constructed with heavy-duty steel frames and metal components will outlast ones made with sub-par parts. When a conveyor has downgraded materials, it will end up costing more in the long run due to added maintenance, repairs, or eventual replacement.
An effective pallet wrapping system relies on speed, efficiency, and quality. By ensuring a pallet conveyor delivers the attributes necessary to attain that, the entire system will operate at peak performance, improving production and revenue.
To learn more about the features & benefits of Orion’s LoPro Triple Drag Chain Conveyor, check out the MA-DX LoPro interactive animation.