When selecting a pallet stretch wrapping system selecting the wrapper itself is the primary concern. You need a machine that can achieve your desired throughput, while also working well with the type of product you’re handling. The conveyor is also a key component in the effectiveness of your stretch wrapping system and should be selected to compliment the wrapper and the product.
Determining the right conveyor for the application, or if a conveyor is even needed, means considering the following factors:
- Load Weight
- Load Composition
- Conveyor Speed
- Loading Height
- Footprint
Load Weight
Both extremely light loads and extremely heavy loads like concrete blocks present challenges. With a typical roller conveyor handling loads of up to 4,000 lbs. some products, like concrete blocks, can hit weights of up to 6,000 lbs. For these products a heavy-duty conveyor is required. An alternative is to eliminate the conveyor entirely and select a wrapper that wraps the load while it is sitting on the floor, with the film carriage rotating around the stationary load. An added benefit is that eliminating the conveyor saves space, as well as the time and expense of installation.
Extremely light loads, like empty plastic bottles or Styrofoam, are also challenging and can benefit from a rotary tower design that wraps the product on the floor. Another option for light loads is the use of a drag chain conveyor. The drag chain eliminates the vibration of roller conveyors and provides smoother transfer of product. This keeps the load from destabilizing before it is wrapped.
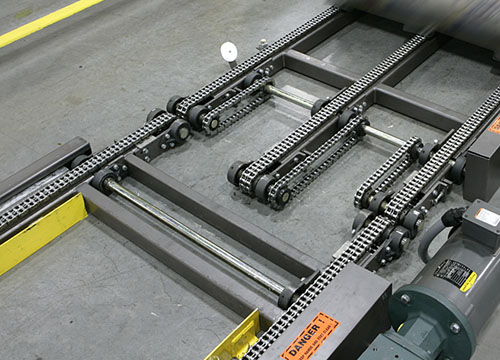
Load Composition
As we mentioned, a drag chain conveyor provides smooth conveyance of light loads, but it also works well for other products that tend to be inherently unstable or fragile. This can include products like bags of mulch or sacks of rice. Even boxes of random mixed loads, which are the norm in beer wholesale distribution, benefit from the drag chain conveyor. In one facility a beer distribution wholesaler reported a 45% decrease in breakage using a drag chain conveyor.
Like light or heavy loads unstable loads are often wrapped directly on the floor with the film carriage rotating around the pallet load.
Another factor in load composition and conveyor selection is the pallet style. The flow of the pallet and position of the bottom boards are important. Chep and GMA pallets are easily run on most styles of conveyor. When it comes to postal or specialty pallets a drag chain or custom conveyor would be the path to look towards.
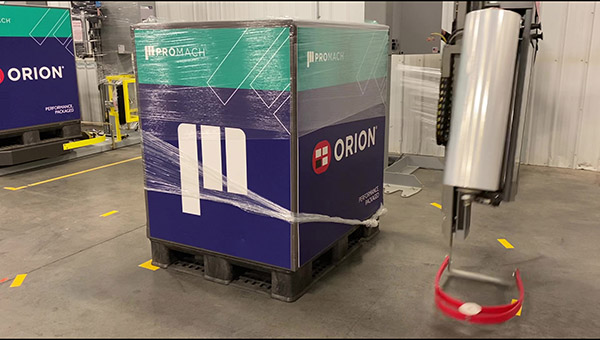
Conveyor Speed
Matching a high-speed wrapper with a conveyor system that can’t match its throughput is a waste of resources. Systems like the dual carriage rotary tower automatic wrapper shown here can handle up to 100 pallets an hour, so using a conveyor with a maximum speed of 30 ft per minute may limit the system throughput. On the other hand, using a conveyor like this low vibration drag chain model, which moves pallets at 60 ft per minute and is able to separate, wrap, and then reconsolidate up to three pallets at a time can help you realize the full potential of the wrapper.
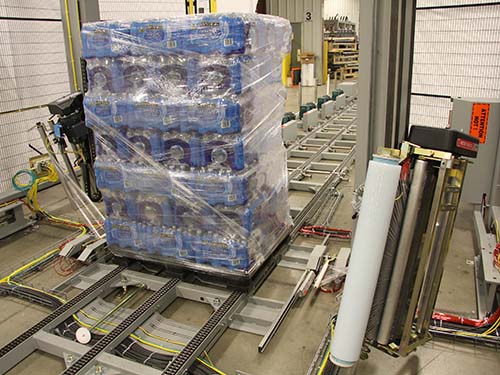
Loading Height
Based on the type of equipment used to transfer pallets in your facility will also help you determine the right conveyor for your operation.
Standard profile pallet conveyors generally stand 18” inches from the floor and are typically loaded using a fork truck or integrated with upstream equipment. They are available in roller or chain designs.
Low profile conveyors range from 4 – 6 inches from the floor. The 4” pass height can utilize the drag chain conveyor whereas the 6” can use the roller type conveyance. This provides universal loading with a forklift, walkie, or pallet jack.
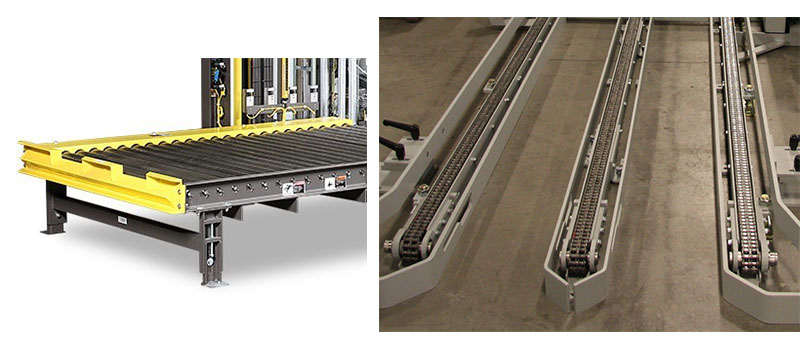
Footprint
Today most pallet conveyor systems have a certain amount of modularity that allows additional sections of conveyor to be added or removed to accommodate your operation’s changing needs. Additionally, features like a 90-degree angle between the infeed conveyor and exit conveyor can help overcome facility space constraints.
We’ve covered the importance of load weight, composition, conveyor speed, loading height, and footprint in selecting a conveyor. While these are some of the main factors there are also considerations such as equipment environment, safety features, load spills and so on, that can impact your selection. Orion Packaging can work with you to make sure you are equipped with the right wrapper and conveyance for your application.